The Technology of Surfing
I was born into a family of surfers. Some of my earliest memories involve the sweet smell of resin, as my father built surfboards on the beach at San Onofre, or in the back yard of our home.
The credit for this is due in part to one brilliant man, Brandt Goldsworthy. In 1941, Brandt taught my dad to surf, to freedive for lobster and abalone, and to build surfboards. By the time I was born, in 1949, the Southern California surfing world was rich and complex, a couple of hundred highly individualistic people spread out from San Diego to Santa Barbara.
My father, Richard Roche, was an ingenious aircraft engineer. When World War II started, he got a job at the Douglas Aircraft Company in El Segundo, California, which is near Los Angeles International Airport. The guy he wound up working next to in the Process Engineering Group, doing materials and plastics engineering, was Brandt, who was one of those guys who really bright people describe as, "WIthout a doubt, one of the smartest people I have ever met."
Brandt's genius was interested in materials, especially resins, exotic plastics, and fiberglass. During the war, Brandt and my dad worked on solving problems for fighter aircraft, making lightweight and durable containers for things.
Brandt later in life
The Douglas manufacturing line in World War IIAs my dad told the story, he and Brandt worked at the aircraft factory from 6 a.m. to 2 p.m. every day. Then they went surfing. And after surfing, they paddled out again, this time with diving masks they made themselves, and dove for lobster and abalone to have for dinner.
From many years before I was born, through my childhood and teenage years, Brandt was over at our house every week, talking with my Dad way into the night. He was one of those people who seemed to emanate blessings and joy in all directions, all the time, while simultanously keeping up an intense technical discussion about engineering.
In those days, if you wanted to surf, you had to build your own board. And, being materials engineers, Brandt and my dad thought about what kinds of materials to use. I do not know if my dad contributed anything to the innovations - he never bragged - but Brandt and one of his buddies, Pete Peterson, did a lot of experimenting and are credited with helping to develop "The California Surfboard," the first lightweight fiberglass board, which was an important innovation. I think Pete gets main credit for building the fiberglass surfboard, with consultation credit going to Brandt.
Greg Noll Steals the Formula
I just found this great footnote in Surfer Magazine online. Link to article.
Noll Steals the Formula
Greg Noll was the third surfboard manufacturer on the California coast to use polyurethane foam when he decided to mold and blow his own blanks.
But first he had to get the correct formula.
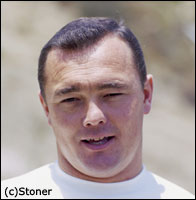
Greg Noll
A strategy behind the free Strohs
So one afternoon he and his father, a chemist, pulled up in front of the house belonging to Hobie’s foam wizard, Gordon “Grubby” Clark. Their motive: industrial espionage cloaked under the guise of a friendly visit. Leave all those spy cameras and sodium penathol and eavesdropping bugs to that Jimmy Bond fella’, thought Noll, all I need is a case of beer to get Grubby talkin’. As Clark moistened his tissues with the free beer, he began spilling the beans. Goaded by Noll, he started rambling on about his foam formula, unaware that Noll senior was linking the molecular tinker toys together in his mind. As Noll remembers it, “Grubby woke up the next morning with a hangover and I woke up with a foam formula.”
The widespread use of polyurethane foam as a surfboard core revolutionized both the sport and surfboard design. Polyurethane foam was lighter and more consistent than balsa wood. Its density could be exactly controlled, and an endless supply of identical blanks would go a long way toward allowing painstaking refinements in design. Rocker could now be easily manipulated and explored, something next to impossible with irregular, organic balsa wood. And most importantly, to the growth of the sport, foam allowed the mass production of surfboards for the first time.
Gordon Clark and Hobie Alter are remembered as pioneers in foam surfboards, but they both give credit to an aerospace engineer named Brant Goldsworthy. A San Onofre surfer, Goldsworthy had come across the new material at a trade show back east; as early as 1938 he had showed the material to Bob Simmons. Goldsworthy, who Clark calls “the biggest heavyweight ever to be involved in the modern surfboard,” had a plastics company that sold components to the WWII aircraft industry. During this period, Joe Quigg, in his quest for better and more durable materials, so diligently hounded the Los Angeles plastics firms that he was suspected to be a German spy. Goldsworthy and partner Ted Thal would eventually become the first to sell fiberglass and resin to the private sector.
Another note, about Pete Peterson, Bob Simmons, and Joe Quigg, from Soul-Surfer. Link.
1946: Fiberglass & Resin
Curiously, the influence that Bob Simmons would have on Joe Quigg -- and vice versa -- did not show itself early on. In fact, in early 1946, when Quigg and his former Santa Monica High School classmate Dave Rochlen visited Simmons at his garage, Quigg found Simmons interesting but far from innovative.
"Dave and I got curious about Simmons," said Quigg of he and Rochlen, who was then on leave from the Marines. "We were still into surfing, and we heard he was building boards in his garage in Pasadena, so we drove over to see what he was up to." They found Simmons in the processs of building three traditional redwood surfboards. "At that time," said Quigg, "he was still selling and talking up big, heavy boards, the same kind we'd always used."
Quigg admitted that, in those days, he wasn't too impressed by Simmons. However, Dave Rochlen said that, "When we first met Simmons, we knew he was different. We knew he was somehow special, and we knew he was up to something. We called him a mad scientist." Importantly, Simmons was just about "the only guy anybody could buy boards from during those [war] years."
At that point, Quigg was more interested in what Brant Goldsworthy, and Ted Thal were peddling, and what the Bakelite Corporation was producing. Goldsworthy and Thal, in the guise of and the Thalco Chemical Company, were the first to sell fiberglass and resin to the private sector and the Bakelite Corporation was the first resin manufacturer.
After initially scoring some catalyst through Dave Sweet's uncle who was in the plastics department of Douglas Aircraft, Joe established a regular connection for fiberglass, resin and catalyst through Ted Thal's office.
.. Fiberglass
The three main components of today's surfboard -- the modern surfboard -- are foam, fiberglass and resin. All three have their beginnings in the wartime technological advances made before, during and following World War II.
"Fiberglass," Stephen Shaw wrote in the first published manual on surfboard making, "is a glass similar to window glass heated to a molten state and strained through very small platinum discs into the air and collected as very fine threads. These threads are immersed in an oil to keep the filaments from breaking as they are woven. The threads are woven on textile machinery, and the oil is melted out under high temperature. A finish, such as Union Carbide's 'Silane' or DuPont's 'Volan' are put on the cloth to promote flexibility and adhesion to the polyester resin. Cloth used in the surfboard industry is woven especially for surfboards."
.. Resin
Fiberglass combined with resin, when activated by a catalyst, can add strength with a minimum of weight.
"Polyester resin," wrote Nick Carroll, "is... a liquid plastic, bulked up by styrene, a benzene derivative that makes up over a third of its content. Various other stabilizers, anti-UV compounds and the like make up the difference. It is turned into a hard plastic by the introduction of a substance known as methyl ethyl ketone peroxide, or 'catalyst,' as we professionals prefer to call it. A small amount of MEKP -- just a few drops per cup of resin -- sets off the hardening reaction..."
"The three resins used in surfboard manufacturing, laminating, hot coating and glossing, are made of a combination of phathalic, anhydride or isothalic acid, makeic and hydride propylene or ethylene glycol and styrene plus a promoter and a catalyst." These "are cooked together forming a long series of molecules. The material is then mixed in the cool state with styrene. With an addition of the catalyst and promoter, the styrene crosslinks the long molecules cooked earlier and form a solid."
Beating Quigg and others to the fiberglass punch, Preston 'Pete' Peterson was the first to build a surfboard -- a hollow board -- using fiberglass, resin and catalyst, in June 1946. Peterson had the help of Brant Goldsworthy, who had a plastics company in Los Angeles that supplied component parts for aircraft in World War II. "The board," wrote Nat Young, "was constructed of two hollow moulded halves joined together with a redwood central stringer and with the seam sealed with fibreglass tape." Goldsworthy's plastics company may have been the same place Bob Simmons scored his fiberglass and resin from, also.
1947: Zahn, Quigg, Kivlin, Rochlen & Melonhead
The Californians that first hit Hawaiian surf following the war included Joe Quigg, Tommy Zahn, Matt Kivlin, Melonhead and Dave Rochlen. They rode the latest in California surfboard design -- Simmons boards.
"It was the late 1940s," remembered Rabbit Kekai. "That's when the first migration of what you call the haoles came. That was Joe Quigg, Tommy Zahn, Matt Kivlin, a guy they called Melonhead and Dave Rochlen. They were the first guys that brought down what we called the potato chip boards; the Simmons." Quigg and Kivlin had, by this time, become associated with Simmons as kind of apprentices, so it was natural that they were riding his designs -- all balsa, encased in fiberglass and resin. Boards made of wood that was 100% balsa had been made before, but never sealed with a compound that completely kept water out of the balsa.
.. Tommy Zahn
It was Tommy Zahn who started the post-war California surfer "cross-pollination." C.R. Stecyk wrote that "Tom Zahn... arrived in Honolulu in 1947" and "immediately lured Joe Quigg, Dave Rochlen and Matt Kivlin to come down soon after. All were armed with provocative, finned balsa Malibu chip surfboards. These wide tailed boards were immediately suspect. Quigg remembers a recurrent phrase of the day being repeatedly uttered, 'Oh, all that balsa, what a waste.' Rabbit who personally befriended the Malibu set, rode their boards, but at that point, characterized them as 'mushers.' The varnished balsa pintail with pine center stringer sported by Quigg employed a dead flat bottom, 50/50 rails and a turned down hard rail in the tail."
"We were amazed to see them on those boards," Rabbit Kekai recalled, "they were just standing at the back end on them because they had those wide tails with just one skeg in the center or concave tails with twin fins. Rochlen and Quigg had twin fins. Kivlin had one of his own single finned boards with a narrower tail."
"Tommy Zahn used to surf with us," Woody Brown told me. "I remember him at Waikiki and he had a balsa board. It was a very light balsa board. See, my board was 80 pounds for those big waves. He had a little board. It couldn't have weighed more than about 30 pounds; all balsa, nothing else. But, it was no good at all at Waikiki, see, with that trade wind blowing.
"We were out one day in pretty big waves; about 20 feet at Waikiki, there. It's called Papa Nui. It's a big blue water break between Queens and Canoes, way out. So, we were out there catching and he couldn't catch 'em. Every time he'd try to catch 'em, the wind would blow him right off the top of the wave. But, with my board, I'd just pop in and go."
Soul Surfer magazine.
Scroll